Solventbased, UV-curable and Latex Inks
DIALUX SI 428
Translucent polyester film, printable on one side for light boxes and other backlit displays.
Printing Systems




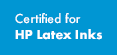
Rolls
Technical data
Characteristic
- Extremely high colour density
- Brilliant, true colour reproduction with or without back lighting (Day&Night).
- Perfect flatness
- Low-reflective printing surface
- Very good temperature resistance
- Certified for HP Latex Inks
Specifications
Coating Printside | satin |
Width (mm) | 1067 |
Thickness | 0.150 mm |
Core Diameter | 76 mm |
Length (m) | 30 |
Opacity | 0.30 |
Base Material | Polyester |
Packing quantity | 1 roll |
Compatibility
- Useable on most large format Ink Jet printers using latex inks.
- Useable on most large format Ink Jet printers using solvent ink systems.
- Useable on most large format Ink Jet printers using UV curing ink systems.
Handling
- Note for Latex-Inks:
To avoid the effect of rewetting (oil film on the print surface due to defective anchorage of ink) it is necessary to establish the optimal drying parameter. This can be done by means of print tests before production print. Rewetting can appear several days after printing when the drying condtions are defective. The rewetting can also be dependent on the given ambient conditions and the composition and consistence of the printing theme. When creating a media profile, this circumstance must be expressly taken into consideration.
- In regard to humidity:
High air humidity during the printing process may lead to banding in the direction of printing and to striations in the print image caused by the transport or press rolls.
- Note for temperature setting:
Before printing you must check that the correct drying temperature has been set by carrying out a trial print. Too high drying temperatures can lead to a deformation of the film which can later cause further problems while processing.
- Note for Drying time / Processing:
The VOC which are contained in solvent and latex inks must be fully dried before further processing. For this reason it is necessary to take long enough drying times into account. The drying time of the printed media depends very much on the quantity of solvent applied. When printing the film in a roll-to-roll process, the printed strip must be unrolled and laid flat as soon as possible until final drying. Solvent residues due to insufficient drying times can lead to blocking during transport in rolled-up form. During lamination such residues can negatively impact the quality of the finished product (flatness, shrinkage behaviour, anchorage, etc...).
- The printed surface must be protected if it is subject over a long time to humidity, abrasion, sweat or other mechanical influences. In the case of unlaminated prints, contact between the print side and the protective screen should be avoided.
- We recommend to use self-adhesive laminating foils for cold lamination or appropriate liquid lamination products.
Storage
- Shelf life: 1 year after delivery
- After printing the remaining roll must be removed from the plotter and stored in its closed original packing in a cool and dry environment.
Downloads (PDF)